Business
Edward Batko’s Zero-Defect Manufacturing Strategies
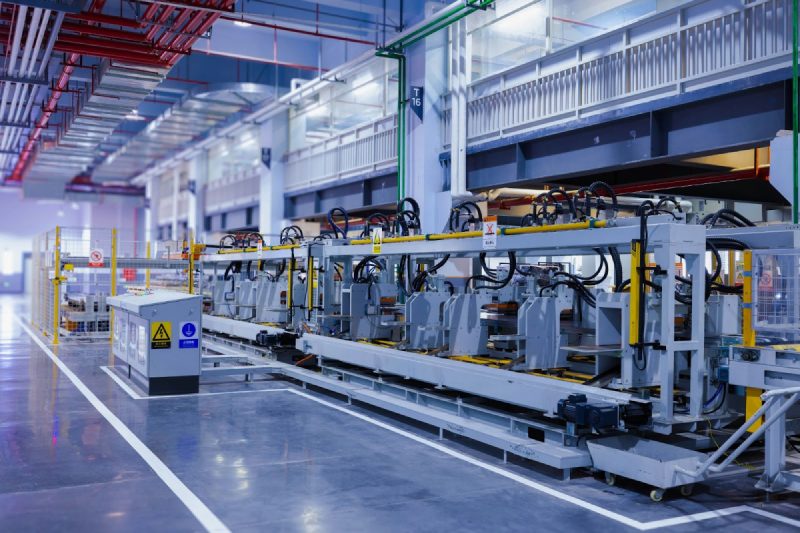
Zero Defect Manufacturing (ZDM) has emerged as a cornerstone of modern production, embodying the pursuit of flawless quality and operational excellence. This approach emphasizes the prevention of defects rather than relying on detection, creating systems that ensure every product meets exact specifications. By combining principles like continuous improvement, workforce empowerment, and the integration of advanced technologies such as artificial intelligence, and predictive analytics, ZDM minimizes inefficiencies and maximizes consistency.
Industries such as automotive, aerospace, and electronics have reaped the benefits of ZDM, reducing waste, boosting reliability, and building customer trust. While challenges like resistance to change and initial costs remain, Edward Batko highlights how the long-term rewards far outweigh these hurdles.
What is Zero Defect Manufacturing?
Zero-defect manufacturing (ZDM) is a quality management approach that eliminates defects in production processes. It is rooted in the philosophy of doing things right the first time, ensuring that every product meets exact specifications without compromising on quality. This is vital in industries where precision and reliability are non-negotiable, such as aerospace, automotive, and electronics.
The relevance of ZDM in today’s manufacturing landscape cannot be overstated. Businesses adopting this strategy experience reduced waste, lower rework costs, and higher customer satisfaction. Companies like Toyota have embraced similar philosophies, demonstrating how a commitment to zero defects can enhance brand trust while maintaining operational efficiency. By prioritizing defect-free production, manufacturers save resources and strengthen their competitive edge in markets where quality is a key differentiator.
Core Principles and Practices of Zero-Defect Manufacturing
At its core, Zero Defect Manufacturing revolves around the principle of prevention rather than detection. This means designing processes and systems that inherently avoid defects rather than relying solely on inspections to catch errors after they happen. This preventative mindset fosters a culture of accountability and precision, ensuring that every production stage contributes to flawless quality.
Continuous improvement is another pillar of ZDM, where manufacturers regularly evaluate and refine their processes to eliminate inefficiencies. Approaches like Six Sigma and Lean Manufacturing reinforce this principle by providing structured methodologies to identify and address variations in production. Such practices have been instrumental in industries like healthcare and automotive, where consistency is paramount.
Organizations embracing these principles often see transformative results, not just in product quality but also in operational performance. By embedding quality into every stage of production, they create systems that are resilient, efficient, and capable of meeting the demands of contemporary markets without compromise.
Key Strategies for Achieving Zero Defects
Designing robust processes is essential for achieving zero defects. Techniques like Failure Mode and Effects Analysis (FMEA) help organizations identify potential points of failure and implement safeguards to prevent them. This ensures that processes are efficient and resilient against errors.
The role of employees cannot be overstated in the journey toward zero defects. Well-trained and engaged workers are more likely to identify potential issues before they escalate, ensuring that quality becomes a shared responsibility across teams. Companies that invest in workforce education often find that empowered employees contribute to innovative solutions and higher overall productivity. Also, fostering a collaboration culture can amplify these benefits, as employees feel more invested in the organization’s success.
Integrating advanced technologies like artificial intelligence and IoT further strengthens defect-elimination efforts. Predictive maintenance systems, for instance, can detect equipment inefficiencies before they lead to product defects. By combining human expertise with technological advancements, manufacturers can create a balanced approach to achieving zero defects, paving the way for sustainable success.
The Role of Data and Analytics in Manufacturing Quality
Data and analytics are the backbone of Zero Defect Manufacturing, enabling manufacturers to detect patterns, uncover inefficiencies, and make informed decisions. Advanced data collection systems and real-time monitoring allow companies to identify deviations from quality standards before they escalate into more significant issues. This proactive approach minimizes downtime and reduces waste, ensuring smoother production cycles.
Analytics tools such as predictive modeling and machine learning algorithms have revolutionized how manufacturers approach defect prevention. These tools can forecast potential failures by analyzing historical production data, enabling timely interventions. Industries like semiconductor manufacturing heavily rely on such systems to maintain rigorous quality standards. Leveraging data enhances product consistency and fosters a culture of continuous improvement. Over time, this reliance on data transforms manufacturing into a more adaptive and forward-looking process, ensuring challenges are met with precision.
Challenges and Solutions in Zero-Defect Manufacturing
Implementing Zero Defect Manufacturing comes with its share of challenges, including high upfront costs and the need for advanced technical expertise. Resistance to change among employees or management can hinder progress, especially in organizations with deeply ingrained traditional practices. However, these hurdles are not insurmountable.
A phased implementation approach often proves effective in overcoming resistance. By introducing new systems gradually and demonstrating their benefits early on, organizations can build trust and buy-in from all stakeholders. Additionally, partnering with external consultants or leveraging existing expertise within the workforce can ease the transition. Some companies have successfully navigated these obstacles by emphasizing the long-term benefits of ZDM, such as reduced operational costs and enhanced customer loyalty. Coupled with strong leadership and clear communication, these ensure that challenges do not derail the pursuit of zero defects.
-
Business3 weeks ago
Prakash and Kamal Hinduja: Driving Social and Environmental Change
-
Education4 weeks ago
Fred DuVal: University Leadership as a Critical Resource for Climate Change Research and Life-Saving Solutions
-
Cryptocurrency3 weeks ago
Designed For The Masses: How Akasha (AK1111) Is Unlocking Crypto For The Next Billion Users
-
Health3 weeks ago
The Hinduja Brothers Commitment to Global Health: Empowering Communities Across Borders
-
Cryptocurrency4 weeks ago
Nexaglobal & Future World Token (FWT): Could This Be the Next Big Crypto Investment of 2025?
-
Startup2 weeks ago
Cost-Saving Strategies Every Small Business Owner Should Know to Boost Efficiency
-
Startup3 weeks ago
Matthew Denegre on the Art of Deal Sourcing: Finding the Right Investment Opportunities
-
Health2 weeks ago
St. John’s Community Health Examines Innovations in Pharmacy Access